נעים מאוד,
שמי גידי חלף, מהנדס תהליך (MSc, BEng) עם ניסיון של כ- 20 שנים במגוון תהליכי פיתוח, גימלון וייצור. בין היתר תהליכי קרוד (ראקציה כימית- USP), קריסט (גיבוש וניקוי- DSP), הפרדות וסינונים בצנטריפוגה, מיצויים צמחיים, תהליכי ניקוי, ייבוש וטחינה (גם רטובה), למינציה, ציפויים ועוד.
הניסיון המצטבר מגיע ממגוון תעשיות, בין היתר: תעשייה כימית, פרמצבטית, בשר מתורבת\ פרמנטציה\ Biomanufacturing, מכשור רפואי, קוסמטיקה, מזון ותוספי המזון, דפוס דיגיטלי ותלת מימד ועוד.
בנוסף, אני בעל ניסיון אישי ויצירת פטנטים במגוון טכנולוגיות: אופן בחירת הטכנולוגיה הנכונה ואופן השימוש הנכון בטכנולוגיה עבור התהליך הרלוונטי (BAT- Best Available Technology). בכל המקרים נדרשתי לפתח טכנולוגיה חדשה לצורך פתרון בעיה בייצור, ובכל המקרים מצאתי טכנולוגיה קיימת ומוכחת שבשימוש, וביצעתי התאמות נדרשות בין התהליך לטכנולוגיה, מה שקיצר משמעותית את זמני הפיתוח, הקל על תהליך הפיתוח והביא לחיסכון גדול בעלויות הפיתוח.
בנוסף, אוכל להעריך היטב את ההיתכנות הכלכלית של מוצר חדש (Techno-Economic Analysis- TEA) בהיבט של תהליך הייצור, התשתית הנדרשת והמוצרים המתחרים, כך שיהיה ניתן בשלבי ההתחלה לכוונן את המוצר ואת תהליך הייצור כך שיהיה כלכלי.
אני גם מלווה תהליכי ייצור ומבצע Tech-Transfer על כל השלבים הנדרשים: כתיבת והעברת הניירת הנדרשת כדי לוודא תיאום ומוכנות של ה- CDMO ונוכחות פיזית שלי כדי לוודא תפעול נכון של מערכות הייצור להשגת איכות וניצולת מיטביים. כולל מציאת CDMO מתאים, בהתאם לצרכי הייצור ולתקציב הקיים.
ובנוסף לכל השירותים הנ"ל אני מבצע וולידציות למערכות ייצור ותהליכי ייצור, כולל כמובן כתיבת הפרוטוקולים והדוחות, ע"פ תקנים נדרשים (IQ/OQ/PQ), Valid Plan, URS, Risk Assessment וכל מה שצריך, בשיתוף פעולה שלי עם מומחים מתאימים.
כמהנדס תהליך וכיועץ מנוסה, אני מתמחה בניתוח ועיבוד של כמויות גדולות של נתונים (Big Data, Process Data Analysis) המתקבלים במהלך התהליך. באמצעות כלים מתקדמים וחשיבה מערכתית, אני מזהה מגמות, אי-התאמות והזדמנויות לשיפור, ומוביל אופטימיזציה (Process Optimization) לייעול, חיסכון ושיפור תפוקות.
צברתי ידע הנדסי נרחב ויכולת תיכנון פיתוח תהליך יעיל ורציף וביצוע אופטימיזציה שכוללת מגוון מערכות ייצור: מכלי בחישה (ראקטורים וביוראקטורים), צנטריפוגה לשיקוע או צנטריפוגה לסינון, מסנן מייבש, מערכות פילטרציה ו- TFF (פילטר פרס, פילטר קרמי, פילטר שק, פילטר צלחת, MF/UF/NF/RO ועוד), אלקטרודיאליזה, משאבות לתהליך, מערכות לטחינה רטובה (מטחנות כדורים), הומוגניזציה ועוד.
יכולת בצוע אופטימיזציה וולידציה לתהליכי ייצור: משטרי בחישה והתאמת נפחי עבודה, תגובות כימיות מגוונות, קריסטליזציה (המסה, הזרעה וגיבוש), תהליכי שיקוע, מגוון אפשרויות סינון, תהליכי ייבוש וטחינה, טחינה רטובה של חומרי הדברה ופיגמנטים, מגוון מיצויים (מיצוי כימי, מיצוי חומר צמחי) כולל שטיפה והפרדת פאזות (מים, שמן, סולבנט), תהליכי נידוף/זיקוק, החלפת ממסים, ניקוי מדיה מחומר מסוים לצורך מחזור המדיה ועוד.
ניסיון עשיר בהגדרת חומרי הגלם וביצוע IPC (in process control- הבדיקות הנחוצות במהלך תהליך הייצור לצורך בקרה על התהליך ומניעת כשלים בייצור), הגדרת הפרמטרים הקריטיים בתהליך הייצור שאחראים לאיכות התוצר בתהליך, הגדרת הפרמטרים המשמעותיים בתהליך הייצור שאחראים לניצולת התהליך ופרמטרים תפעוליים שמהווים פקטור בנוחות הייצור אך ללא השפעה על האיכות והניצולת.
Education:
2004-2006- MSc., Hebrew University, Biochemistry & food science.
1999-2003- BEng., Ben Gurion University, Biotechnology Engineering.
WO2022238867A1, WO2023156933A1 Systems and methods for recycling cell culture medium (Includes Perfusion with a centrifuge, Pilot Scale)
US11067922B2 Intermediate transfer blanket
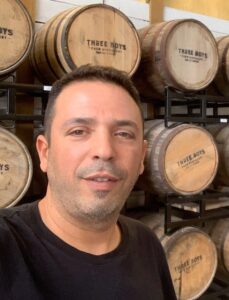
שירותים:
ייעוץ ופיתוח עבור מגוון תהליכי ייצור
ניסיון מגוון בפיתרון בעיות כגון: הזנה, בחישה, משטרי טמפרטורה, הפרדה, סינון, ייבוש, טחינה ועוד.
לכל שלב בתהליך הייצור, מוקדם ככל שיהיה, ישנה השפעה על המשך התהליך ועל איכות התוצר הסופי. מניסיוני המצטבר אוכל לוודא ולאפטם את תהליך הייצור ומערכת הייצור לצורך יציבות התהליך.
כיועץ, אתה מגיע לרצפת הייצור ממוקד בפיתרון הבעיה, עם ראייה רחבה וניסיון קודם, אשר תורמים משמעותית בהבאת הפיתרון המתאים עם היתרונות והחסרונות הקיימים.
ביצוע הוכחת היתכנות (POC) ופיתוח תהליך
ביצוע POC מהיר לצורך אישור אבן דרך. ה POC נעשה בצורה אופרטיבית כך שלאחר מכן ניתן לגמלן את התהליך ללא שינוי בקונספט התהליך.
העברה מפיתוח לייצור\ Scale Up
בחינת הפרמטרים בתהליך במעבדה, בחינת הפערים בין מערכת הייצור במעבדה לבין מערכת הייצור בפיילוט, בניית דוח פרמטרים לתהליך, בחינת הבדיקות הרצויות לצורך שליטה על התהליך (IPC), בניית Specification למוצר ועוד.
ביצוע גימלון לתהליך בהתאם לדרישות, בחינת אפשרות העלאת קיבולות במערכת הייצור הנוכחית. ניסיון אישי רב בגימלון בתעשיה הכימית (חומרים פעילים בתעשייה הכימית: ייצור, גיבוש, ייבוש ועוד), precise fermentation, מגוון מיצויים כימיים וצמחיים, ייצור ג"לים ועוד. כולל העברת חלקית או מלאה של תהליך מנתי לתהליך רציף.
Tech Transfer
עבור מפעלים בארץ או עבור העברת הייצור לחו"ל. כולל בחינת התהליך והכנת הניירת הרצוייה. ניסיון אישי בהעברה וקבלת תהליכי ייצור מארה"ב, הודו, סין, איטליה, גרמניה ושוויץ (מגוון תהליכי ייצור ומערכות ייצור).
בחינת שיפורים טכנולוגיים משמעותיים לתהליך הייצור: אופטימיזציה ואיתור טכנולוגיה מתאימה
להלן מספר דוגמאות:
- שיפור פרוצדורת סינון לצורך הורדת עלויות הסינון, ע"י שיפור אופן ביצוע הסינון בעזרת ביצוע פרה פילטרציה עם פילטרים מתאימים או הורדת החלקיקים בעזרת שיקוע בצנטריפוגה.
- שיפור פרוצדורת השיקוע לצורך שיפור גודל חלקיק שיבוא לידי ביטוי בזמני הפרדה, שטיפה וייבוש.
- ביצוע הפרדה בעזרת סינון (לדוגמא פילטר פרס) במקום שיקוע בדיקנטר, לקבלת תוצאות מיטביות שנמדדות באיכות, ניצולת וקיבולת מערכת הייצור.
AI וניתוח נתונים לשיפור תהליכים
ניסיון בניתוח נתוני תהליך (Big Data) בעזרת AI, Python ו-Excel לשיפור ביצועים, חיזוי תקלות, ואופטימיזציה חכמה לקבלת החלטות תפעוליות.
בחירת טכנולוגיית BAT מותאמת לתהליך
ניסיון באיתור והטמעה של Best Available Technologies (BAT) בהתאם לאילוצים רגולטוריים, כלכליים ותפעוליים, תוך השוואת חלופות והערכת עלות-תועלת.
ניתוח טכנו-אקונומי (TEA) לתהליכי פיתוח של מוצר חדש
ניסיון בביצוע Techno-Economic Analysis (TEA) להערכת כדאיות תהליכים וטכנולוגיות, כולל CAPEX, OPEX, ROI והשוואת תרחישים לפיתוח וקבלת החלטות, בהיבט של עלויות ייצור פר תהליכי ייצור ומוצרים מתחרים שקיימים בשוק.
ליווי הייצור אצל קבלני משנה בארץ ובחו"ל
- עבור ייצור של פעם אחת או ביצוע קמפיין.
- עבור ייצור מוצר אחד או מגוון מוצרי החברה.
- כולל וידוא ביצוע הכנות לייצור באתר של הקבלן בהתאם לצורך.
- הכרה אישית של כמה יצרני משנה בכמה מקומות באירופה ובהודו.
ביצוע ואלידציות- למערכת ולתהליך PQ/OQ/IQ, Valid Plan, URS, Risk Assessment
- כתיבת פרוטוקולים ודוחות בהתאם לתקנים הנדרשים ובהתאם לצרכי החברה (מוצר פרמצבטי, ציוד רפואי, קוסמטיקה, מזון).
- עבור כל שלבי תהליך הייצור והמערכות הנלוות.
- החל מהגדרת צרכי המערכת, בחינת קבלת המערכת אצל היצרן ועד להתקנה וולידציה מלאה באתר הייצור, בהתאם לצרכי החברה.
הרצאות והדרכות לצוותים
- כיצד מפתחים תהליך ייצור?
- כיצד מעבירים תהליך מפיתוח לייצור?
- הבדלים בין פרמטרים קריטיים, משמעותיים ותפעוליים בתהליך?
- כיצד בונים פרוטוקול ייצור?
- כיצד מבצעים וולידציה לתהליך?
- תכנון ניסויים לצורך קבלת החלטות נכונות.
דוגמאות
בזכות הניסיון בפיתוח תהליך והעברה מפיתוח לייצור של מגוון מוצרים, צברתי ידע קריטי לגבי השפעת שלבים מוקדמים בתהליך הייצור על המשך תהליך הייצור ועל המוצר הסופי. במרבית הפעמים שיש צורך בשיפור שלב בתהליך הייצור, השיפור יגיע בשלבים מוקדמים יותר בייצור כדי לבוא לידי ביטוי בהמשך התהליך. להלן מספר דוגמאות מעשיות:

דוגמא 1:

לאחר שיקוע וגיבוש שלב הסינון והשטיפה מאוד ארוכים (לא מיצוי צמחי שמכיל מגוון חומרים שנמצאים בצמח, אלא חומר אחיד עם רמת ניקיון גבוהה).
פירוט:
שלב הסינון והשטיפה מאוד ארוכים עקב בריחת חלקיקים קטנים דרך בד הסינון או לחלופין עקב "אטימות" עוגת הסינון ולכן ההזנה נעשת לאט בלחץ נמוך. בסיום ההזנה מוזנת השטיפה, שהיא גם איטית ולא יעילה ופריקת עוגת סינון מאוד רטובה כתוצאה מהחלקיקים הקטנים. בנוסף, ייבוש ארוך שבסיום מתקבל חומר גושי, לא הומוגני ועלייה באי ניקיונות ופגיעה בפולימורף במהלך עיבוד המוצר (ייבוש וטחינה).
הפתרון:
הגדלת גודל החלקיק כדי שהממס יוכל לעבור סביב החלקיק בקלות וכך ניתן יהיה לשטוף ולסחוט את העוגה היטב. חלקיק מאוד קטן מקשה על סינון, שטיפה וסחיטת העוגה, ומביא לעוגת סינון מאוד רטובה שמביאה ליצירת גושים במהלך הייבוש הארוך. בנוסף, הייבוש הארוך מביא לעליית רמת האי ניקיונות ופגיעה ביציבות המוצר לאורך זמן.
פתרון נוסף אם אפשרי הינו חומר עזר לסינון, אך החומר עזר נשאר בעוגת הסינון, במידה ועוגת הסינון הינה התוצר אז יש למצוא פתרון גם לזה.
לסיכום:
גידול גודל החלקיק לפני שלב הסינון הביא לעליה באיכות התוצר וקיצור משמעותי בזמני הסינון, שטיפה, ייבוש, ושיפור הניצולת, האיכות והיציבות הכימית של המוצר. גיבוש נכון=חלקיקים גדולים= סינון ושטיפה מהירים ויעילים= סחיטה טובה בסיום= ייבוש מהיר לאבקה= איכות כימית ויציבות משופרים, עלייה בניצולת וקיצור זמני הייצור (עלייה בקיבולת הייצור במערכת).
הערה:
כאשר מדובר בקשיים בסינון של מיצויים צמחיים או שומניים, ניתן להשתמש בחומרי עזר לסינון אשר מקלים מאוד על רמת הג'לטיניות של העוגה ומביאים ל"אווריריות" מסוימת בעוגת הסינון ומקצרים משמעותית את זמן הסינון ואת איכות הסינון.
דוגמא 2:
איפטום תהליך ייצור קיים של מיצוי חלבון שמופק מצמחים לצורך גימלון המערכת פי 5.
פירוט:
לצורך הכרת התהליך לפני גימלון נעשה MASS BALANCE והשוואה בין מגוון מנות הייצור הקיימות במערכת.
הפתרון:
בניתוח הפרמטרים במנות הייצור נמצאו הבדלי ניצולת משמעותיים בין מנות גדולות למנות קטנות: למנות גדולות, שנעשו בתדירות נמוכה, היו ניצולות גבוהות יחסית למנות קטנות. נראה שהפערים נבעו משלב השיקוע לפני ההפרדה בצנטריפוגה: במנות גדולות נעשו 2 פריקות בצנטריפוגה וניתן לראות שעבור אותו הנפח בפריקה השנייה מתקבל תוצר/פלט גדול יותר יחסית לפריקה הראשונה. שיפור שלב השיקוע לפני ההפרדה בצנטריפוגה (solid bowl) הביא לעליה משמעותית בניצולת הייצור והמשך השיפור הגיע מהגדלת נפחי העבודה במיכלי הייצור.
לסיכום:
עלייה משמעותית בניצולת התהליך ובקיבולת מערכת ייצור ע"י שיפור השלב הרלוונטי בתהליך. בנוסף, תיכנון נכון של קמפיין הייצור (ייצור מנות ברצף) הביא לשיפור משמעותי בקיבולת הייצור של המערכת.
דוגמא 3
שבירת תאים במהלך ההפרדה בצנטריפוגה.
פירוט:
לעיתים המוצר אינו רק מוצק אלא תא או אצה עם חשיבות לשמירת תכולת התאים. במקרים כאלה יש לבצע הפרדה באופן עדינה עם פחות כוחות גזירה כדי שהמוצקים יופרדו ולא ישברו ביציאה\בפריקה, שכן במידה והתאים נשברים אז תכולת התא יוצאת עם ה"פאזה הקלה" והולכת למעשה לאיבוד.
הפתרון:
בחינת מיקום שבירת התאים בצנטריפוגה (כניסה, שהייה, יציאה), בחינת טווחי מהירות הצנטריפוגה שנדרשת להפרדה טובה והיתר זה התאמות רצויות.
לסיכום:
ניתן להפריד מוצקים וגם תאים שבירים שרגישים לכוחות גזירה, ואף לבצע פרפוזיה, בצנטריפות solid bowl לאחר ניסוי וטעייה ומציאת נקודת עבודה מתאימה.
דוגמא 4
זמני טחינה רטובה ארוכים, עליה בטמפרטורה בזמן הטחינה וחוסר יציבות המוצר.
פירוט:
במהלך טחינה רטובה יש לטחון עד לרמת גודל חלקיק רצוי. זנבות של חלקיקים גדולים שבמדיה פוגעים ביציבות המוצר מפני שהחלקיקים ממשיכים לגדול והמוצר אינו עומד ב specifications המוגדרים לאורך חיי המדף של המוצר (גודל חלקיק, זרימות ועוד).
הפתרון:
יש לוודא שהמטחנה מלאה בכמות רצוייה של כדורים ובגודל המתאים לצורך קבלת גודל חלקיק מתאים בפרוצדורת הייצור הקיימת. פרוצדורת הטחינה צריכה להתאים למערכת (טחינה בסחרור- מיכל ומטחנה: טחינה במעבר ממיכל למיכל - מיכל, מטחנה ומיכל נוסף: טחינה במיכל עם מטחנה - BASKET MILL). ברוב המקרים יש להתחיל את הטחינה בסל"ד נמוך מכיוון שבתחילת הטחינה משתחררת הרבה אנרגיה שמובילה לחימום המדיה (בד"כ עלייה בטמפרטורה אינה רצויה). לאחר הורדת גודל החלקיק באופן משמעותי אך עדיין לא מספק, ניתן להגביר את סל"ד המטחנה לצורך קבלת גודל חלקיק רצוי, מבלי לפגוע באיכות המוצר.
לסיכום:
יש לוודא שפרוצדורת הטחינה מתאימה עבור המוצר והמערכת. חשוב לעשות את ההתאמות הרצויות לצורך קבלת מוצר רצוי. חשוב לעבור על נתוני מנות הייצור שמתקבלות כדי לוודא שאותה פרוצדורת טחינה מביאה לקבלת מוצר דומה.
דוגמא 5
הקמת מערכת איוד אטמוספרית לצורך צמצום השפכים במפעלים שמייצרים שפכים (עלויות פינוי גבוהות).
פירוט:
פינוי שפכים מלווה בהוצאה כספית גבוהה מאוד, גם אם אחוז המוצקים שבגינם יש צורך לשלוח לפינוי קטן.
הפתרון:
פיתוח מערכת איוד אטמוספרית שיכולה לעבוד 24/7 שדומה מאוד לאופן שבו הריאות בגופינו עובדות: רשתות במקום ריאות, ספרינקלרים לצורך הרטבת הרשתות ומפוח לצורך מעבר אוויר בקונטיינר- הכנסת האוויר נעשת בלחות סביבתית והוצאת האוויר הינה ב 90-95% רוויה (הגעה ל- 100% רווייה ביציאה דורשת הגדלת המערכת לאינסוף).
לסיכום:
פיתוח מערכת איוד אטמוספרית, זולה וקלה לתפעול, שנועדה למקומות עם לחות יחסית נמוכה עם קבוע אידוי מאוד יעיל.
דוגמא 6
סילוק אי ניקיון ממדיה לצורך שימוש או שימוש חוזר במדיה.
פירוט:
כאשר קיים אי ניקיון במדיה שמונע את היכולת להשתמש שוב במדיה נרצה לסלק את האי ניקיון עד לרמה שאינו יפריע למדיה תוך איבוד מינימאלי מנפח המדיה וממרכיבי המדיה הנוספים. תהליך ניקיון תמיד מלווה באיבודים נוספים שנרצה למזער אותם. חשוב לאפיין נכון את האי ניקיון כדי למצוא את ההבדלים המשמעותיים בינו לבין יתר מרכיבי המדיה על מנת שתהליך הניקוי יהיה אופרטיבי והדיר (מסיסות, גודל, מטען וכדומה).
הפתרון:
מציאת ממברנות מתאימות או חומר ספיחה רצוי כך שסילוק האי ניקיון יעשה בצורה מהירה, אופרטיבית והדירה.
לסיכום:
חשוב למצוא את ההבדלים הכי משמעותיים בין האי ניקיון ליתר המדיה כך שהתהליך יהיה יעיל, קל לתפעול והדיר. לפעמים יש לעשות טיפול מקדים למדיה לצורך הבלטת האי ניקיון כך שניתן יהיה לסלקו בקלות מהמדיה.
דוגמא 7
עלויות סינון גבוהות.
פירוט:
סינון מהווה במרבית הפעמים גם צוואר בקבוק לתהליך וגם עלות משמעותית בייצור. לרמת הסינון הנדרשת ולתכונות המדיה יש חלק משמעותי בכך.
הפתרון:
ביצוע פרה פילטרציה בעזרת מערכות מתאימות, ובתנאים המתאימים, שבהן עלויות העבודה זניחות (כגון פילטר פרס, צנטריפוגה טובולרית, spiral wounds) אך בסיום העבודה, מתקבלת מדיה מוגדרת שקל לסנן אותה באופן קל ומהיר. גם אם הסינון הסופי הנדרש הינו 0.2 מיקרון, ניתן לעשות פרה פילטרציה במערכת רלוונטית כך שהתסנין בסיום יעבור פילטרציה סטרילית, 0.2 מיקרון, במהירות ובקלות.
לסיכום:
ניתן לבחון מגוון דרכים להורדת עלויות הפילטרציה ולהשתמש במגוון טכנולוגיות בהתאם לדרישות ולמגבלות הקיימות.
דוגמא 8
ניקוי חלבונים בתהליך אופרטיבי בקיבולות גדולות.
פירוט:
ניקוי חלבונים יכול להיעשות בכמה דרכים ומומלץ למצוא את הדרך המתאימה עבור התהליך הרצוי. ניתן לנקות חלבונים ע"י הזנת המדיה לקולונה שמכילה מדיה (שרף) שקושרת לחלבונים, יחד עם זאת, ניתן לנקות חלבונים בדרכים אופרטיביות יותר, במידה ונמצא שהחלבונים עמידים לתהליך החלופי.
הפתרון:
לקיחת המדיה שמכילה את מגוון אי הניקיונות והחלבונים למערכת TFF מתאימה (Tangential Flow Filtration). התאמת המערכת מבוססת על חומר מבנה הממברנה וגודל הפורות. באופן שכזה ניתן "לכלוא" את הפרקציה הרצויה ולהיפטר ממגוון אי הניקיונות (MF, UF, NG, RO). ניתן להוסיף דיאליזה לתהליך לצורך הגדלת רמת הניקיון של החלבונים.
לסיכום:
ניתן לבחון דרכים אלטרנטיביות ואופרטיביות לניקוי החלבונים בקולונות לצורך הורדת עלויות התהליך והתאמתו לקיבולות הרצויות. יש לוודא כמובן את אי רגישות החלבונים ולהתאים את התהליך למוצר. לצורך היתמודדות עם כוחות גזירה שפוגעים בחלבונים ניתן להישתמש ב- Cassettes or Hollowfibres שמביאים לכוחות גזירה נמוכים משמעותית מ Spiral wounds שבו משתמשים לדוגמא לניקוי חומצה לקטית בקיבולות גבוהות.
ניהול פרוייקטים
ניהול פרויקטים והקמת מערכות ייצור אצל קבלן מתאים-עד לוולידציה של המערכת והתהליך:מערכת לייצור חומר פעיל בתעשייה הכימית
מערכת לניקוי חלבונים
תיכנון והקמת מערכת לאיוד שפכים אטמוספרית ייחודית
מגוון ראקטורי נירוסטה עבור נוזלים וחומרים סמיכים
מערכת ייבוש למוצר ייחודי
הקמת מערכות טחינה רטובות
תיכנון והקמת מערכות פילטרציה
רכישה של מגוון צנטריפוגות וציוד הפרדה מתאים
רכישת מערכות ייצור
מיכלי בחישה, צנטריפוגות סינון או שיקוע (כולל דיקנטר), מערכות פילטרציה מגוונות (סינון קרמי, פילטר פרס ועוד: Dead end or tangential flow), מערכות טחינה רטובה (מטחנה במיכל או בסחרור), משאבות גזירה, ייבשנים (וואקום, מגשים, מצע מרחף) ועוד. כולל עזרה באיפיון ציוד הייצור המתאים.
רכישת ציוד ייצור בד"כ מלווה בהמון לבטים והתייעצויות מסיבות ברורות: עלויות רכישה גבוהות, זמני אספקה ארוכים, עלויות אחזקת הציוד והחשש שהטכנולוגיה לא מתאימה. רכישת צנטריפוגה מיצרן אירופאי מוביל צפויה לעלות עד פי 4 לעומת יצרן מהמזרח וזמן האספקה ארוך משמעותית גם כן. בהרבה מאוד מקרים היצרן האירופאי מייצר בעצמו במזרח. אני אוכל לתת כמה אפשרויות רלוונטיות (יצרן מוביל, יצרן מהמזרח וציוד משומש במידה וקיים), וללוות אתכם בהתאם לצורך, ברכישה, בהפעלה הראשונית ובואלידציה של המערכת. עבור כל ציוד שתרצו, יהיה ניתן למצוא מגוון יצרנים במזרח שאף יעשו התאמות למערכת שלכם, בהתאם לצורך. גם עבור מיכלים מכל הסוגים, צנטריפוגות (פילטרציה, שיקוע, טובולרית ועוד), דיקנטרים, מטחנות יבשות ורטובות, מגוון מערכות פילטרציה (פילטר פרס, פילטר שק, קרטריג', הולופייברים), בוחש נייד לקובייה, מערכות ייבוש, גרנולטור או אקסטרודר ועוד.
ולידציות
ביצוע ולידציה למערכת ולתהליך הייצור (PQ/OQ/IQ):
- עבור מגוון מערכות: מכלי ייצור, ביוראקטורים, צנטריפוגות, משאבות, יבשנים, מערכות טחינה רטובה ויבשה, מערכות סינון ועוד.
- עבור מגוון תהליכי ייצור: חומרים פעילים לתרופות, מגוון מיצויים, אימות ניקיון במעבר ממוצר אחד לאחר, ניקוי מדיה ו purification ועוד.
- עבור העברת תהליך הייצור למפעל אחר, בארץ או בחו"ל (Tech Transfer).
University
שיקולים בתכנון מיכלי בחישה, בוחשים, תהליכי גיבוש וטכניקות הפרדה
כמהנדס תהליך מנוסה עם ניסיון בתכנון מיכלי בחישה, מחומרי מבנה מתאימים, עבור מטרות מגוונות, הייתי מעורב בפרויקטים רבים בתעשיות שונות כגון התעשייה הכימית, טכנולוגיות מזון, פרמנטציה\ביוטכנולוגיה (חלבונים, שמרים, בשר מתורבת) ומיצוי חומרים פעילים. להלן שיקולים מרכזיים בתכנון מיכלי בחישה: יחס קוטר\גובה במיכל, בחירת בוחשים מתאימים וגובה הבוחש במיכל, מידת הצורך חימום\קירור ויחס שטח\נפח לצורך השליטה בטמפרטורה, אופטימיזציה של תהליכי גיבוש וקבלת החלטות מושכלות בין שיקוע לסינון כטכניקות הפרדה. כאן אציג כמה היבטים מכריעים בהנדסת תהליכים באמצעות שילוב של תובנות תיאורטיות ודוגמאות מעשיות.
תכנון מיכל בחישה: עיצוב מיכל בחישה ממלא תפקיד מרכזי בהשגת בחישה יעילה והעברת חום ומסה אחידה וגם הכנסת כוחות גזירה לתמיסה. גורמים כגון גיאומטריה של המיכל ושוברי זרימה הם קריטיים. לדוגמה, בתעשייה הכימית, בחירת הגיאומטריה של מיכל הבחישה עשויה להיות מושפעת מהצורך ביעילות בחישה והומוגניות התמיסה בעוד שבתעשיית הפרמנטציה ביוטכנולוגיה הדגש הוא יותר כוחות גזירה נמוכים ועל שמירת סביבה סטרילית ויכולת ניקיון קלה וטובה למניעת זיהום (פחות שוברי זרימה, בוחש עם כוחות גזירה נמוכים וכדומה).
בחירת הבוחש הנכון: בחירת בוחש מתאים חיונית כדי להבטיח משטרי זרימת נוזלים אופטימליים ויעילות בחישה. יישומים שונים דורשים סוגים שונים של בוחשים, כגון עוגן, טורבינה או מדחפים. בתעשיית המזון, למשל, ייצור תחליבים או תרחיף משוקע עשוי לדרוש מערבלים בעלי כח גזירה גבוה ובנוסף בוחש מנגב, בעוד שבתעשיית הפרמנטציה חומרים שלא רגישים לגזירה ניתנים לבחישה בבוחש Rushton ואילו לרגישים לגזירה נבחר בוחש Pitched blade or Marine type.
אופטימיזציה של גיבוש: גיבוש הינו תהליך חיוני בתעשיות החל מכימיקלים ועד תרופות. השגת גיבוש מבוקרת דורשת הבנה של גורמים כמו מסיסות, קצבי קירור וטמפרטורת נוקלאציה. לדוגמה, מגזר התרופות עשוי להזדקק לבקרה מדויקת כדי לייצר גדלי חלקיקים עקביים ופולימורף מסוים ואף לעשות הזרעה כדי לשלוט באופן הדיר בתהליך הגיבוש.
בחירה בין שיקוע לסינון: ההחלטה בין שיקוע לסינון כטכניקות הפרדה תלויה בגורמים כגון התפלגות גודל החלקיקים, אופי החלקיק (קשיח או "ג'לטיני"), והאם החלקיקים מהווים את המוצר בסיום התהליך או מסיימים את התהליך. במיצוי של חומרים פעילים, שיקוע עשוי להתאים לחלקיקים גדולים יותר בעלי צפיפויות שונות, בעוד שסינון יכול להיות מועדף בתעשייה הכימית עבור חומרים שעברו גיבוש.
להלן מספר דוגמאות מעשיות:
תעשייה כימית: בייצור פולימרים, תכנון מיכל בחישה עם אימפלר סרט סלילי יכול להבטיח העברת חום יעילה, מה שמוביל להדירות באיכות המוצר.
טכנולוגיית מזון: בעת יצירת רטבים או נוזלים, בוחשים בעלי גזירה גבוהה עם אימפלרים מיוחדים מסייעים להשיג הומוגניות ולמנוע הפרדת מרכיבים.
ביוטכנולוגיה: בתהליכי תסיסה, בחירת עיצוב בוחש מתאים ומבנה המיכל היא חיונית לשמירה על מעבר חמצן ולמיטוב צמיחת התאים\חיידקים.
מוצקים מרחפים: בהקשר לטחינה רטובה- דיספרסר לצורך גזירת המרכיבים (טחינה רטובה, חומרים פעילי שטח, חומרים מסמיכים וכדומה), הוספת שוברי זרימה או מיצוב הבוחש בזווית.
מסקנה: תכנון מיכלי בחישה, בחירת בוחש, יחס שטח\נפח פני המעיל קירור\חימום, אופטימיזציה של גיבוש ובחירת טכניקות הפרדה הינם היבטים בסיסיים של הנדסת תהליך בתעשיות מגוונות. המומחיות והניסיון שלי בתחומים אלה, מאפשרת לי לספק ללקוחות שירותי ייעוץ הנדסי יקרי ערך, שישקללו את מגוון הצרכים והשיקולים, למערכת ייצור מתאימה. על ידי הבנת הפרטים הקטנים של צרכי הלקוח ושל תהליך הייצור, אני יכול לסייע במציאת פתרונות מתאימים קיימים או חדשניים, התואמים את הצרכים הייחודיים של המוצר, מבחינת איכות, הדירות, תפוקה ויעילות הייצור.
תכנון נכון של ביוראקטור
ביוריאקטורים הינם כלים חיוניים בתחום הביוטכנולוגיה, ומשמשים במרכזם של תהליכים שונים של תסיסה, תרביות תאים ועוד. כדי לתכנן ביוריאקטור יעיל, יש לקחת בחשבון מספר גורמים קריטיים כגון: ביצוע עיקור ללא תקלות (שטח פנים מינימאלי של פנים הביוראקטור שבו סיהום יכול לשרוד), ערבוב מיטבי לצורך בקרת חומציות, טמפרטורה, וספיגת חמצן טובים, תוך מזעור כוחות הגזירה. כיצד ניתן לעשות זאת? להלן מספר דרכים כך שמהלך התיכנון יעשה בצורה נכונה (וזאת בהנחה שמדיית הגידול מאופטמת גם כן):
- תכנון הבחישה הינה פעולה בסיסית בתכנון ביוריאקטורים, שכן זה מבטיח את ההומוגניות של מדיום הגידול, מונע שקיעת תאים ומאפשר העברת מסה וחום יעילה. הנה כמה שיקולים חיוניים לתכנון בחישה יעילה:
- בחירת אימפלר: בחירת האימפלר היא קריטית. סוגים שונים, כגון טורבינות ראשטון, אימפלרים ימיים וטורבינות להבים משופעים, מציעים רמות משתנות של מערבולות וגזירה. יש לבחור את האימפלר המתאים לצרכי התהליך כדי למזער את הנזק לתאים. יחד עם זאת, במידה ובוחש שנחשב יעיל יותר אינו פוגע בתאים אז מומלץ להישתמש בו לצורך יעילות בחישה מיטבית.
- מהירות האימפלר (Impeller Speed): המהירות שבה האימפלר מסתובב משפיע על כוחות הגזירה בביוריאקטור. מהירויות נמוכות יותר עדיפות לתאים שרגישים מאוד לגזירה, בעוד שמהירויות גבוהות יותר עשויות להתאים לתאים שפחות רגישים לגזירה. כוחות הגזירה שמופעלים על התא קשורים גם לצמיגות המדיה. ניתן לשלב בין כמה גורמים כך שלמרות שצמיגות המדיה תרד, התא יחווה פחות כוחות גזירה.
- אימפלרים מרובים: ניתן להשתמש במספר אימפלרים ברמות שונות בתוך הביוריאקטור כדי לשפר את אחידות הערבוב מבלי להעלות באופן משמעותי את כוחות הגזירה.
- ספיחת חמצן- חמצן חיוני לגדילה ולחילוף החומרים של מיקרואורגניזמים ותאים. להלן מספר דרכים שיעזרו לשפר את ספיחת החמצן במדיה:
- מיקום ה Sparger משפיע באופן משמעותי על קצבי העברת החמצן.
- ניטור ובקרה: השתמש במערכות בקרת משוב כדי להתאים את קצבי האוורור בזמן אמת, ולהבטיח אספקת חמצן אופטימלית.
- בקרת קצף: הקצפה עלולה לעכב את העברת החמצן. הטמיעו חומרים יעילים נגד הקצפה ואסטרטגיות בקרה כדי לשמור על רמת הקצפה נמוכה. גם כאן ניתן להוריד את רמת ההקצפה ע"י פרמטרים תהליכיים ולאו דוקא ע"י שימוש בחומרים פעילי שטח שמונעים הקצפה מצד אחד אך אינם טובים לגידול התאים כאשר הסיבה העיקרית לשימוש הינה מניעת ההקצפה.
- כוחות גזירה עלולים לפגוע בתאים ובחלבונים רגישים, ולסכן את התהליך הביולוגי. להלן שיטות למזעור כוחות הגזירה:
- אימפלרים שמביא לבחישה יעילה תוך הכנסת כוחות גזירה נמוכים כגון אימפלרים של משוטים.
- שלוט בזהירות במהירות האימפלר כדי למנוע גזירה מוגזמת שתפגע בקצב גידול התאים או לחלופין, תביא ליצירת חומרים לא רצויים יצירת סטרס שבו נמצא התא.
- בזמן תיכנון המיכל יש לתכנן נפח בחישה מתאים כך שהבוחש יהיה טבול היטב במדיה. במידה ולצורך קבלת בחישה יעילה יש להגיע ל RPM גבוה, ניתן לחלופין לייצר קומה נוספת לבוחש כך שיהיה בוחש תחתית ובוחש אמצעי, ושניהם יחד יספקו בחישה טובה בסל"ד נמוך (מניעת מהירות קצה גבוהה).
תכנון עובי צנרת במערכת ייצור פשוטה ובסיסית (לדוגמא מיכל ייצור עם מערכת CIP ומיכל הזנה וכדומה):
תכנון עובי צנרת במערכת ייצור פשוטה כרוכה במספר שיקולים להבטחת הבטיחות והיעילות של המערכת. להלן שלב אחר שלב שיעזור לתכנן את הצינור וקוטרו בהנדסה כימית:
- הבנת דרישות התהליך: קביעת את אופי הנוזל (קורוזיבי, שוחק וכו ') ואת תנאי ההפעלה (טמפרטורה, לחץ, קצב זרימה) של המערכת.
- בחירת חומרים: תכונות חומר: בחר חומרים התואמים לנוזל, תוך התחשבות בגורמים כמו עמידות בפני קורוזיה, תכונות מכניות ועמידות לטמפרטורה.
- חישוב לחץ התכנון והטמפרטורה:
- לחץ תכנון: קבע את לחצי ההפעלה המרביים והמינימליים.
- טמפרטורת תכנון: חשב את טמפרטורות ההפעלה המרביות והמינימליות.
- חישוב עובי הצינור: מתח אורכי: השתמש בנוסחאות מהקוד הרלוונטי כדי לחשב את עובי הצינור הנדרש בהתבסס על מתח אורכי. לדוגמה, ב- ASME B31.3, השתמש בנוסחה לעובי עיצוב לחץ. לחץ היקפי: חשב את העובי הנדרש כדי לעמוד בלחץ היקפי, בהתחשב בגורמים כמו לחץ פנימי ומומנט עקב עומסים חיצוניים.
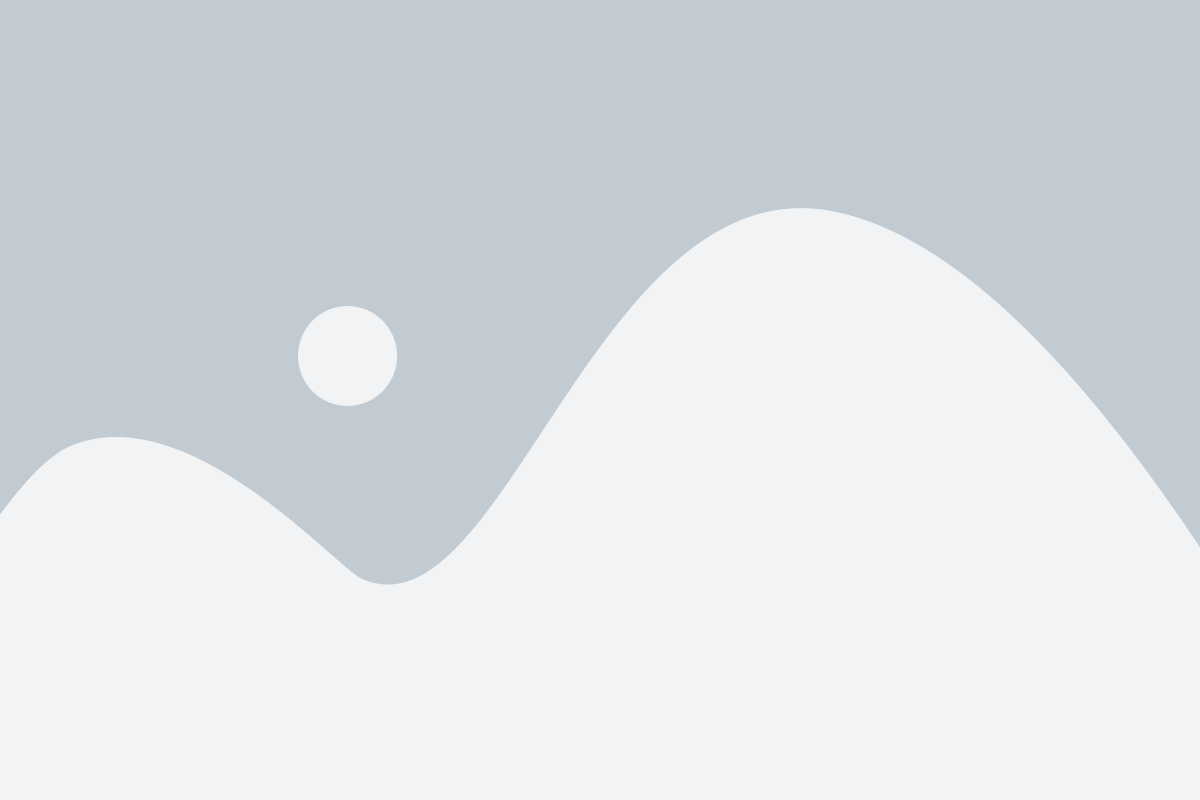